Autonomous Spacecraft Testing of Robotic Operations in Space (ASTROS)
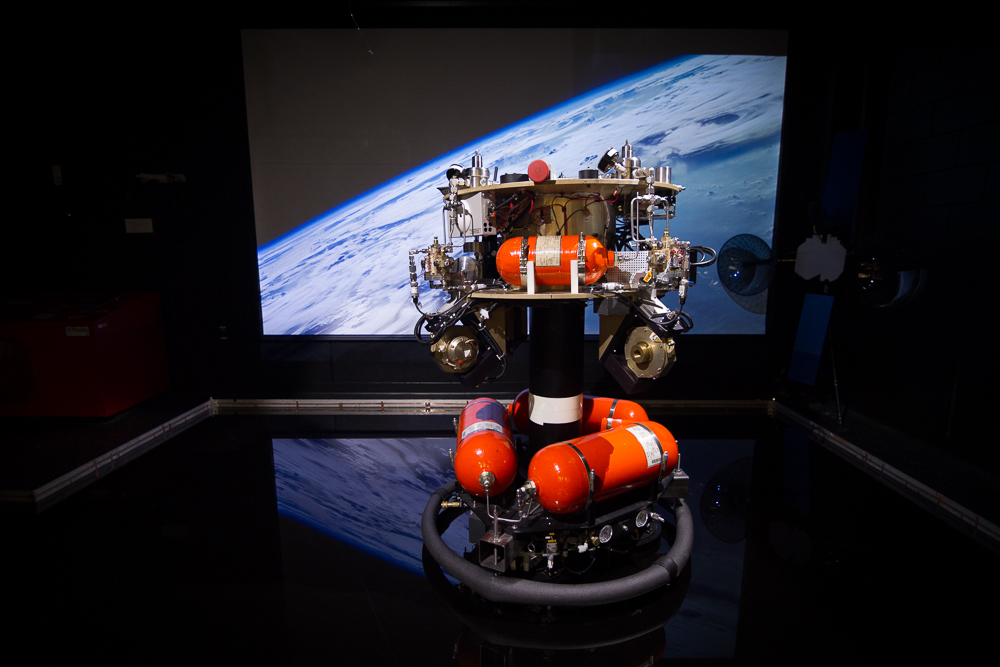
Autonomous proximity operations, including the capability for timely, on-demand, on-orbit servicing and refueling of space assets, are deemed as an enabling factor advancing the current civilian and military capabilities in terms of information gathering, space asset upgrading and maintenance. Such activities are inscribed in the larger realm of space robotics, applying modern autonomous robotics methods to achieve difficult and sensitive tasks, all the while diminishing the reliance on ground segment human-in-the-loop interference.
The Autonomous Spacecraft Testing of Robotic Operations in Space is a 5DoF spacecraft simulator and frictionless motion experimental platform facility. Its objective is to validate and evaluate the performance of guidance, navigation and control (GNC) algorithms designed for in-space rendezvous, using dedicated hardware. The goal is to achieve space-like test conditions to simulate the motion of spacecraft under the authority of an on-board GNC algorithm.
The experimental facility is composed of a test arena, where experiments are performed, and a control room where users monitor and command the execution of the developed algorithms via a development computer. The test arena is a 4m x 4m (14ft x 14ft) flat epoxy floor over which experimental platforms can hover without any friction.
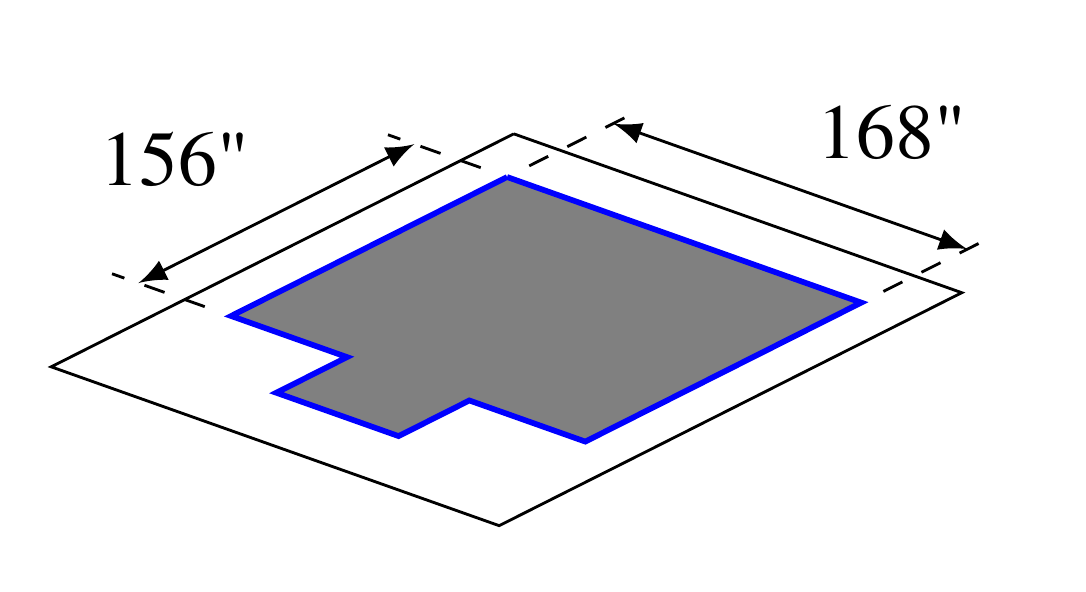
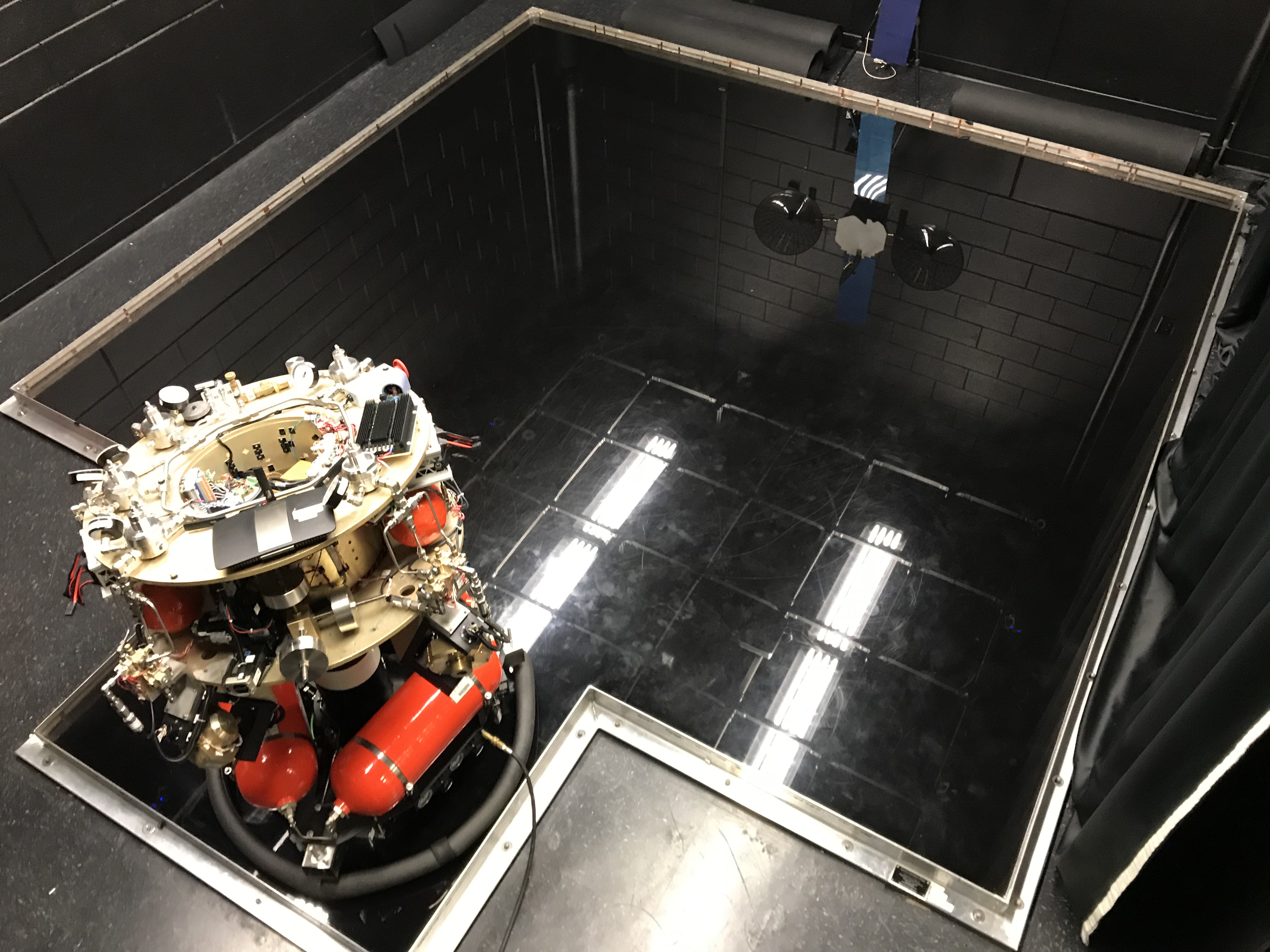
Additionally, dedicated lights on scaffolding help to mimic space-like lighting conditions in the visible spectrum.
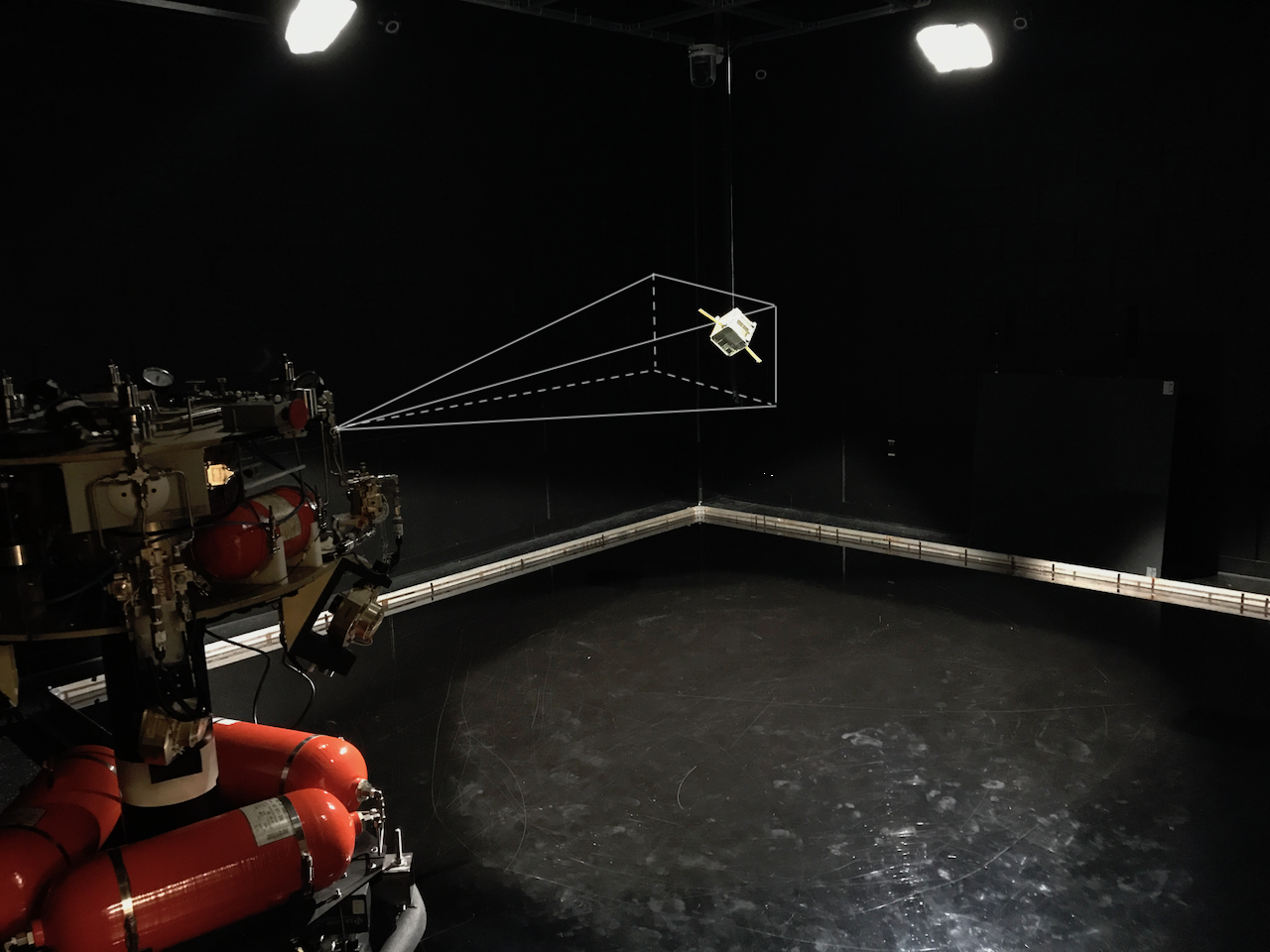
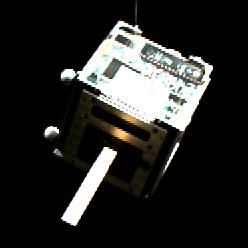
The ASTROS test platform comprises two segments: the lower and upper stages. These stages can be operated in a pure rotation mode, a fully connected mode or a full 5DoF mode, depending on which segments are being levitated.
The lower stage of the platform is equipped with 4 high-pressure air tanks storing up to 3300psig, 3 linear air bearings and a hemispherical air bearing. The linear air bearings levitate the 450 lbs test platform off the epoxy floor by a height less than the width of a human hair and, in doing so, provide 2 degrees of freedom in translation across the test arena, as well a degree of freedom in rotation. The hemispherical air bearing situated at the top of the lower stage provides a near-perfect spherical surface, which in turn levitates the upper stage by means of high-pressure air.
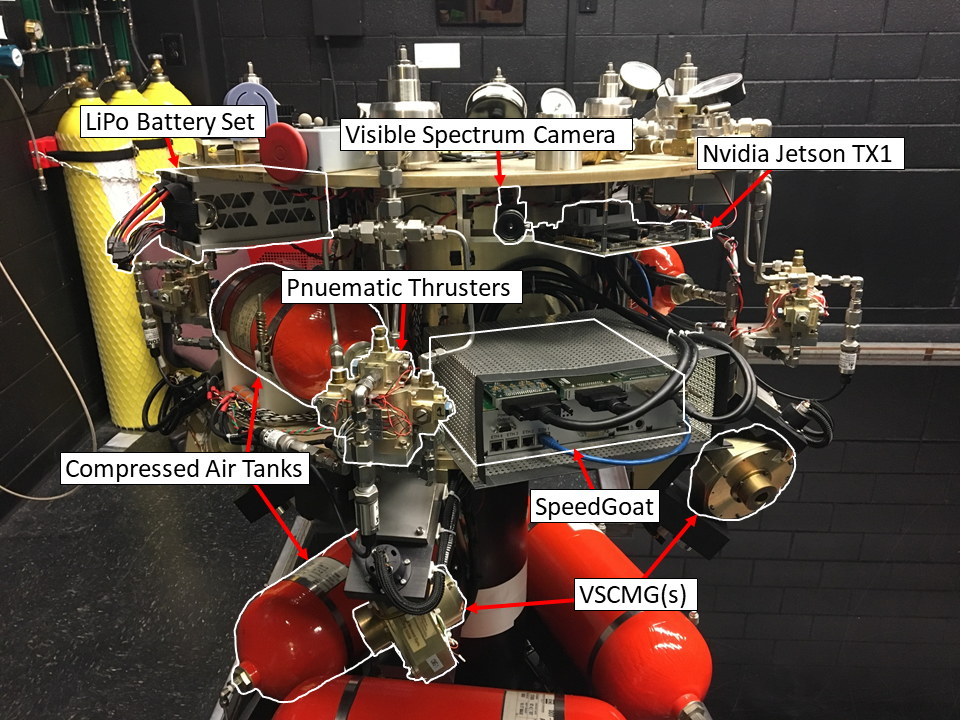
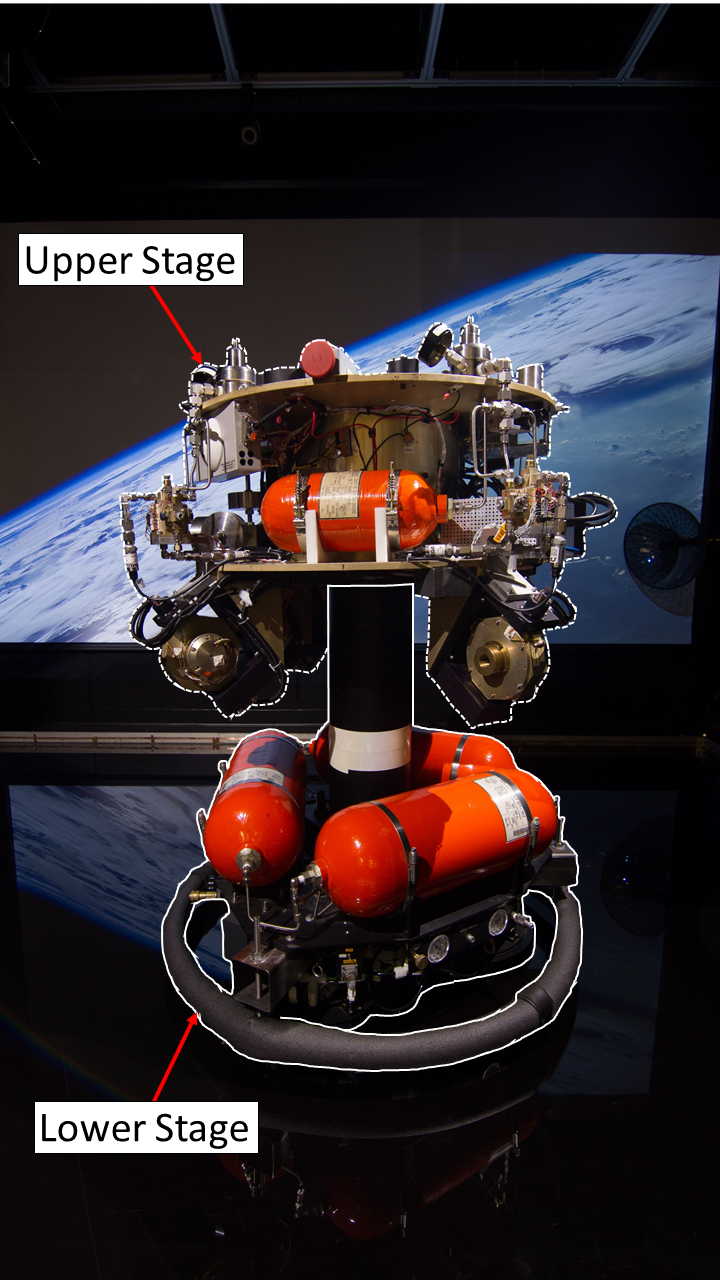
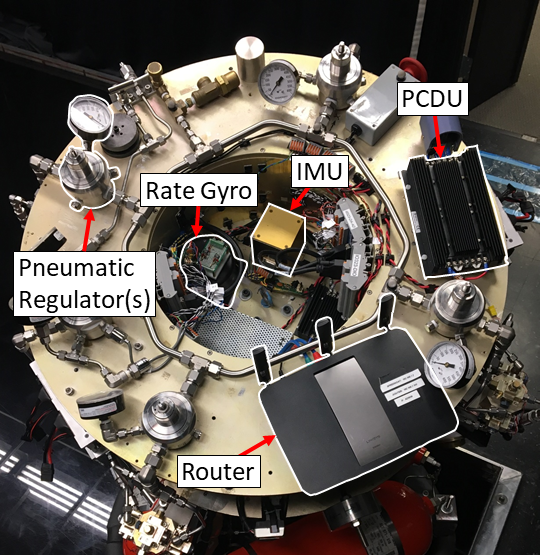
The upper stage of the platform sits on the lower stage using a near-perfect spherical cup and, when levitated, provides the additional 3 degrees of freedom of rotation. This stage also houses the essential systems for sensing, computation and actuation. Indeed, 12 pressurized air thrusters, arranged in a 3-3-3-3 configuration provide individually 5 lbf of force, modulated by an implemented 10Hz pulse width modulation (PWM). These 12 thrusters, each capable of being actuated individually or in group, impart the change in linear and angular momentum required to follow a reference trajectory. A further two air tanks store the energy required for actuation of the thrusters, to which air is circulated using a high-pressure air regulation system.
Furthermore, a set of 4 variable-speed control moment gyros (VSCMGs), arranged in a pyramid configuration, provides additional torque using momentum exchange, thus reducing the use of thrusters for controlling the rotation of the upper stage. Using two motors, each VSCMG is capable of generating gimbal velocity (change in direction of angular momentum) and wheel acceleration (change in magnitude of the angular momentum vector), using dedicated Roboteq DC Motor drivers. Four lithium-polymer batteries store the electrical energy required to actuate the VSCMGs, activate the thruster solenoids. The upper stage also comprises a suite of electronic components: power conditioning and distribution units (PCDUs), auto-balancing linear stage motors, on-board computers, communication interfaces (USB, RS-232, RS-458, GPIO) and dedicated sensors.
Among the equipped sensors, we count a three-axis inertial measurement unit (IMU), a rate gyro (RG) and a two-axis inclinometer. A visible-spectrum camera, an infra-red camera (projected) as well as a time of flight (ToF) camera are also included in the upper stage. The latter enable perception algorithms to be tested on the platform directly, using an Nvidia Jetson TX1 micro-computer. With this dedicated computer, applications that require fusion of data from multiple sensors or heavy image processing can also be tested on-board.
The designed GNC algorithms are compiled and executed on a SpeedGoat MATLAB Simulink real-time target computer housed in the upper stage. By interfacing with the target computer via WiFi, the users can quickly prototype algorithms within the commonly used Simulink environment on the development computer and remotely upload, compile and execute the desired maneuvers on the ASTROS platform.
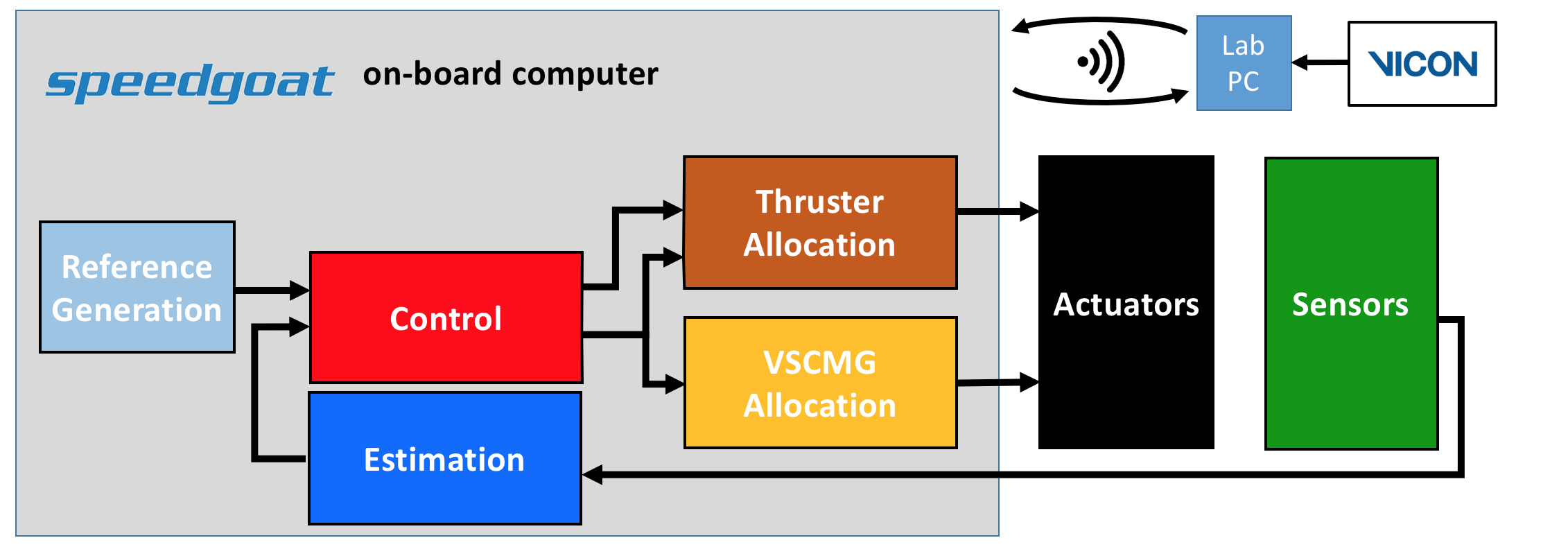
Sponsors
This project has been made possible via an AFOSR DURIP award.
Selected Publications
- Cho, D., Jung, D. and Tsiotras, P., "A 5-dof Experimental Platform for Spacecraft Rendezvous and Docking,'' Infotech at Aerospace Conference, Seattle, WA, April 6-9, 2009, AIAA Paper 2009-1869.
- Tsiotras, P., "A 5DOF Experimental Platform for Research in Spacecraft Proximity Operations,'' AAS Guidance and Control Conference, Breckenridge, CO, Jan. 31-Feb. 5, 2014, AAS Paper 2014-114.
- Valverde, A., Filipe, N., Kontitsis, M. and Tsiotras, P., "Experimental Validation of an Inertia-Free Controller and a Multiplicative EKF for Pose Tracking and Estimation Based on Dual Quaternions,'' 38th AAS Guidance and Control Conference, Breckenridge, CO, Jan. 30-Feb. 4, 2014, AAS Paper 2015-017.
- Dor, M., and Tsiotras, P., "ORB-SLAM Applied to Spacecraft Non-Cooperative Rendezvous,'' AAS Spaceflight Mechanics Conference, Kissimmee, FL, Jan. 8--12, 2018.